Even when CNCs are equipped with automatic post-process gaging systems, there are always a few important adjustments that must be done manually. Don’t take operators understanding these adjustments for granted. #cnctechtalk
Making sizing adjustments is one of the most important tasks a CNC operator must master. Even when CNCs are equipped with post-process gaging systems that automatically update the CNC with offset changes for critical surfaces, there are always a few important adjustments that are not automatically done. Do everything you can to ensure that CNC operators are able to perform this critical task. 2 Flute End Mill
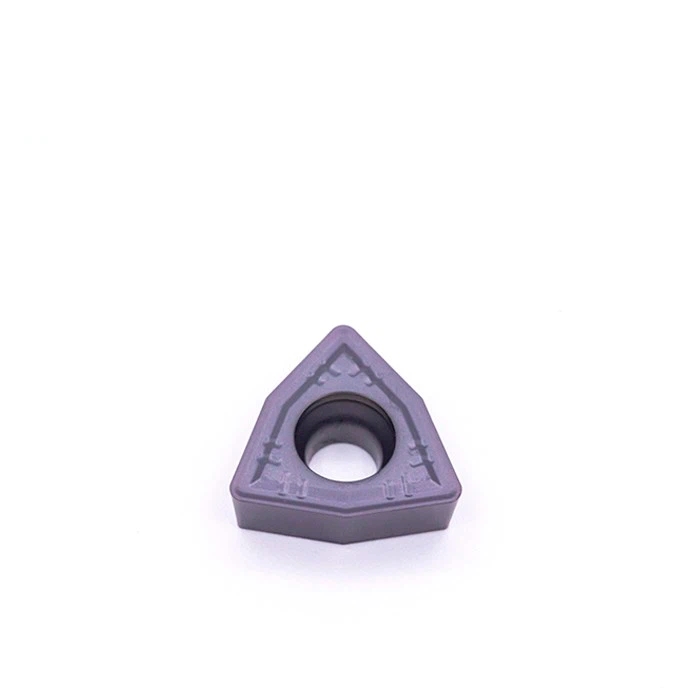
Explain that the need for sizing adjustments is caused by four issues, three of which are handled by the setup person when running the first workpiece in a production run:
Relate how setup people use trial machining techniques to “size in” each tool while running the first workpiece. If they do this correctly, the first workpiece will be a good one, and the production run will begin with all machined surfaces being machined very close to their intended sizes (target values).
CNC operators must know that their sizing-adjustment involvement is related to tool wear, which is most pronounced with single-point cutting tools like turning tools and boring bars. It causes machined surfaces to grow or shrink in the direction of the cutting tool. Depending on the tolerance involved, tool wear can cause a surface to grow or shrink out of its tolerance band over time. The CNC operator must make a sizing adjustment before this occurs.
With small lots and short machining cycles, tool wear will not be an issue. All workpieces will be finished before critical surfaces grow or shrink out of tolerance. More to the point, it is often a highly skilled setup person who runs out the job when only a few workpieces must be produced. A lesser-skilled operator will not be involved.
The larger the lot size and the longer the machining cycles, the more likely it becomes that tool wear must be dealt with. With large lots, jobs are often turned over to a lesser-skilled operator. This operator must possess many of the same sizing-adjustment skills a setup person utilizes when making adjustments during setup.
To make a sizing adjustment for a given surface, the operator must know, or be able to determine, at least five things:
It can be frustrating when operators master the first four steps only to mess up at the finish line. If the operator makes the adjustment using the wrong polarity, of course, the cutting tool will adjust in the wrong direction — machining too much material and causing a scrap workpiece, or not machining anything at all.
Explaining the polarity of a sizing adjustment for some machines and machining operations is easy. With most operations performed on a machining center, the rule-of-thumb is: For most machining operations, if the cutting tool must machine more material, the adjustment polarity will usually be negative. If it must machine less material, the adjustment polarity will usually be positive.
Consider any depth-machining cutting tool such as a drill, tap or end mill. Tool wear will cause the depth surface to become shallower over time. More material must be machined, and the adjustment polarity will be negative. When an end mill machines the contour of an internal pocket, tool wear causes the pocket to become smaller. Again, more material must be machined, and adjustment polarity will be negative.
But any rule-of-thumb has exceptions. To fully understand sizing adjustment polarity, operators need to know more. With depth surfaces machined on machining centers, for instance, they must understand a bit about the polarity of the involved axis: the Z-axis. Machining downward into the pocket requires a negative movement in the Z-axis. So, to go deeper, the adjustment polarity will be negative.
Now consider a back-spot-facing tool that moves a pilot through a hole before the cutting edge is deployed. This cutting tool machines in the Z-axis positive direction. For this kind of tool, machining more material will require a Z-axis adjustment in the positive direction.
Understanding axis polarity as it relates to making sizing adjustments is even more important with turning centers. Even with a simple two-axis lathe, cutting tools can (and often do) machine in just about every direction.
With the X-axis, it is relatively simple. Consider turning or boring critical diameters. Operators must understand that the X-axis is the diameter-controlling axis. Machining larger in diameter (in both cases) requires a positive X-axis adjustment polarity.
It is more challenging when machining in the Z-axis. Moving toward the workholding device is the negative Z-axis direction. If machining toward the workholding device, machining more material requires a negative polarity. But if machining away from the workholding device (back turning), machining more material will require a positive polarity.
Don’t take operators understanding these important concepts for granted. Not understanding them has resulted in many a scrap workpiece.
Tips for establishing and maintaining a regular gage calibration program.
For CNC operators, sizing adjustment is an essential skill. Keep these points in mind when training new CNC users.
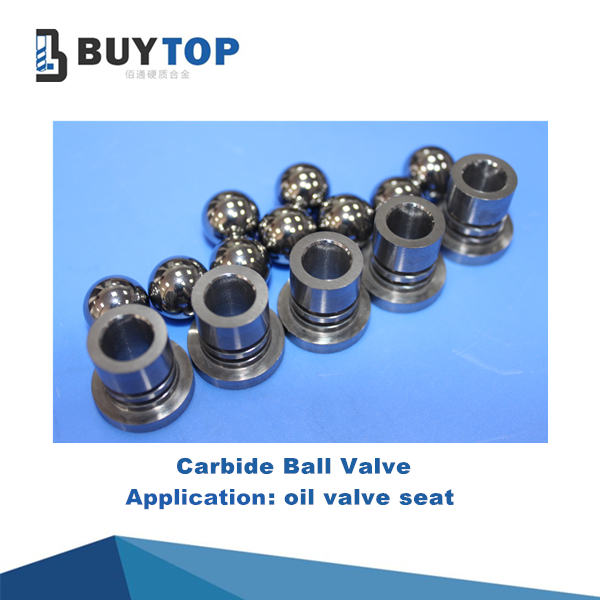
Flute End Mill Gage capability programs can help analyze the cause of stability problems, but it can be revealing to manually sketch out histogram data to get a pictorial view of what is happening.