Thyssenkrupp and Wilhelmsen launched a 3D printing joint venture aimed at providing 3D-printed spare ... [+] parts to the maritime industry.
Mechanical parts wear out and break. It happens to cars, planes, and factory equipment. But when it happens to a cargo ship miles from shore with a load of products due halfway around the world, it can quickly become a million-dollar problem. 607 Opc Drum
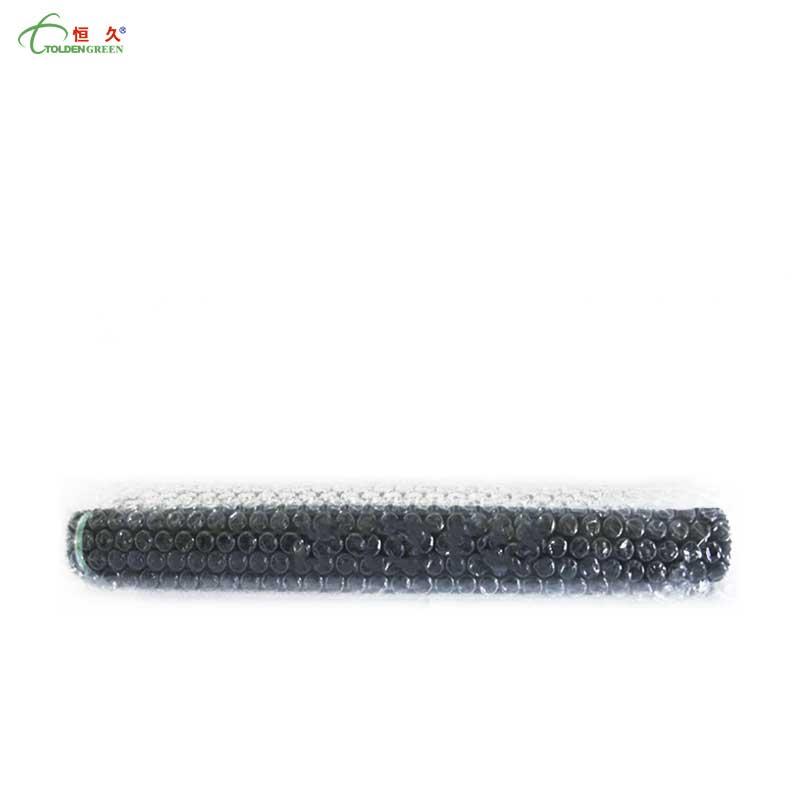
It’s a scenario that marine industry leaders Thyssenkrupp Materials Services, the material distribution and supply chain wing of Thyssenkrupp, and Wilhelmsen Ships Service know well. They’ve invested substantially in 3D printing technology as a solution. They’ve used it to manufacture critical spare parts faster and cheaper than traditional manufacturing and have even dropped 3D-printed parts onto a vessel from a drone. Anything to keep ships moving.
Earlier this month, these two billion-dollar, hundred-plus-year-old multinationals teamed up to offer the global maritime industry a cutting-edge, on-demand digital manufacturing platform for 3D-printed spare parts.
Wilhelmsen, which aims to further the digital transformation of the maritime industry, especially for spare parts, chose to partner with Thyssenkrupp for its strong engineering expertise in industrial 3D printing, also called additive manufacturing.
Three years in the making, the new platform called Pelagus 3D will “deliver maritime spare parts more efficiently in terms of time and cost, allowing customers to ensure their vessels’ seaworthiness and keep their operations moving on schedule,” according to Thyssenkrupp.
Both Thyssenkrupp and Wilhelmsen have been 3D printing spare parts for ships and offshore installations for at least five years. They’ve made metal propellers, impellers, gears, and nearly any part that can break, plus less conspicuous parts out of engineering polymers that can also cripple a vessel’s operation.
The new venture opens up this spare part service to more end-users (vessel managers) and vessel part makers (OEMs) with a network of about 60 additive manufacturing service providers onto one digital platform.
By digitizing and decentralizing part production, Pelagus 3D aims to disrupt the entire ecosystems of the maritime and offshore supply chain.
But it’s far more than an online spare part catalog. OEMs, such as Kongsberg Maritime, which makes propulsion systems for cruise ships, ferries, and navies, can upload the digital files of their parts to the platform so that manufacturing partners around the world (or the one closest to the point of need) can 3D print them on demand. Vessel owners can also upload digital part files to be manufactured, but since most end users don’t have digital files, Pelagus 3D can help with 3D scanning and redesigning the required parts, especially for obsolete components.
“Our Pelagus 3D engineers work together with both end users and OEMs to ensure that the digital files are redesigned to ensure that the spare part performs better or the spare part is printed in another material that helps prevent corrosion (for example),” says Kenlip Ong, CEO of Pelagus 3D. “When end users submit a query for a part, there are steps to indicate the issues that the current part faces and our engineers will proceed to work closely with them to solve the issues that they face.” In other words, with data on why the part failed, the new part can be made better not just reproduced.
Why would ship builders and marine equipment makers want to upload digital files to the Pelagus 3D platform instead of manufacturing and selling them to vessel managers directly?
OEMs, such as Kawasaki, which makes propeller blades among other parts, have joined the platform to get parts to customers faster and cheaper, but also reduce their own costs and stay competitive.
Part makers can eliminate the costs surrounding logistics and standing inventories, plus deliver better parts in new materials. Digital files enable an OEM to make a better part each time it’s printed. They can also customize and consolidate parts to improve functionality and increase overall performance.
Customer can also choose to have their spare parts in materials not previously available, such as high-performance plastics that are as chemical- and heat-resistant as metals but much lighter weight.
3D printed parts also enable OEMs to boost their sustainability profile. The technology uses less material and wastes less material in manufacturing compared to forging, casting, and milling. The ball valve from Wilhelmsen pictured below, for example, was designed by Valland SpA, 3D printed by Thyssenkrupp, and made with recycled metal from start-up F3nice sourced from upcycling out-of-service metal spare parts from decommissioned ships.
A 3D-printed marine ball joint was installed in the field.
“Through the usage of cutting-edge additive manufacturing technology, we were able to solve part performance issues by improving the reliability and durability of the component,” Wilhelmsen said in a post.
For vessel managers, the benefits are clear. On top of cost and speed and a nearly infinite catalog of spare parts, in many cases, having Pelagus reengineer and 3D print one failed component can prevent the replacement of an entire mechanical system.
“When spare parts are obsolete, we work together with the end users and OEMs to create digital files of the old spare part and design it in a way that makes it more durable and with a better performance. We ensure that end users do not need to replace a whole piece of equipment,” says Hakon Ellekjaer, Chief Commercial Officer of Pelagus 3D.
All 3D printed parts go through a quality assurance process at each stage of the manufacturing according to additive manufacturing and maritime industry part standards. This platform's traceability ensures that the quality of the fabricated products can be replicated worldwide.
Adherence to industry-established standards and engineering support are where Pelagus 3D is trailblazing a path for spare part digitalization for other industries.
A recent report from the auto collision repair industry found that 3D printing will revolutionize the marketplace for spare parts for auto repairs, but holding it back is the lack of manufacturing to industry standards.
In transportation, military, aviation, any sector that relies on spare parts to keep it functioning, physical inventory is quickly becoming a thing of the past. Digital catalog solution providers, such as 3YourMind, Castor, and Spare Parts 3D, can comb through an OEM’s existing inventory of parts and point out the ones that can be 3D printed to the same or better quality than the parts made with traditional manufacturing. In this analysis step, companies can find parts and components that could be improved with 3D printing.
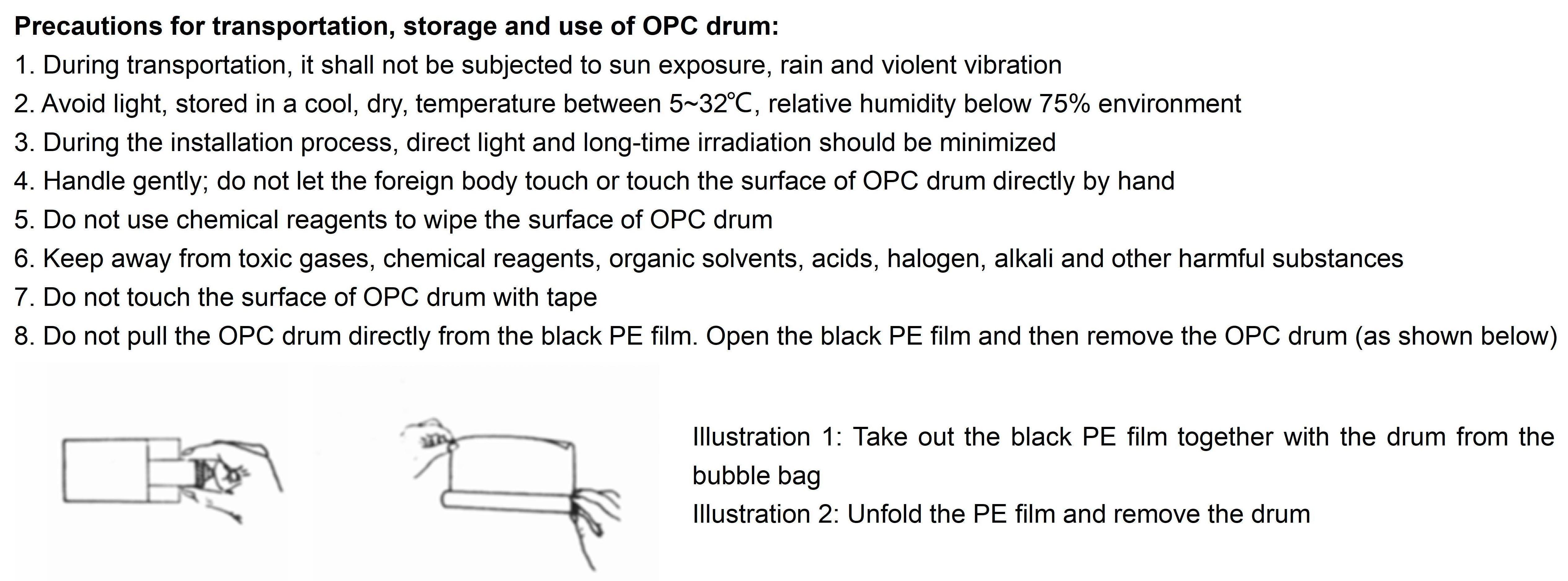
Organic Photoconductor As more companies explore the advantages of on-demand additive manufacturing for faster, localized part production, and continuous design improvement, the promise grows for smoother, more efficient global supply chains.